You are here: / Home
Test procedures for electrical components
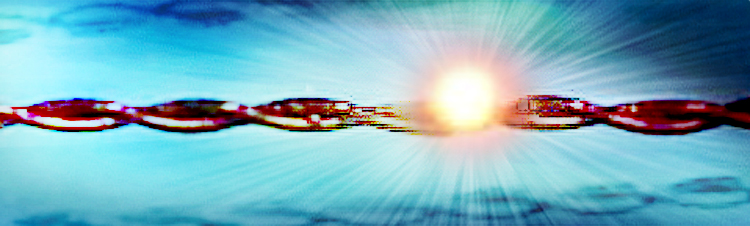
Bundesministerium für Wirtschaft und Technologie
03/2011 – 06/2013
Dr. Roland Müller
+49-351-4081-772
finished
Insulating properties of hermetic compressors
Corona resistance of coated / enameled wires in refrigeration engineering
Specific and efficient test procedures are required for machines, components and materials in electric drive technologies. ILK Dresden has years of experience in testing dielectric strength and insulating properties, disruptive discharge voltage and compatibility of materials. A main focus consisted in the development of methods of complex (thermal-chemical-electrical-mechanical) aging of components and materials for the electric drive and refrigeration engineering.
Especially in refrigeration engineering the environmental requirements increase due to the framework legislation of the European Union (F gases regulation, MAC directive). Besides the necessary change to refrigerants with a Global Warming Potential less than 150 there are efforts to increase the tightness of refrigerating systems by means of half or full hermetic compressors.
The ILK has developed methodic test standards and measuring devices for these new generations of mobile and stationary, directly electrically driven compressors, which comprises the components in contact to the refrigerant and detect undesirable interactions safely and reliably (sealed tube test). Wires, insulating coatings, all materials of rotors and stators and the working media were considered to be the critical components. As a result of a R&D-project custom-designed test methods and robust verification procedures were developed for proving the quality of the working fluids and the materials of electric compressors, which are also sensitive to possible aging symptoms of the refrigerant-lubricant-system.
Among these methods the investigation and evaluation of the quality and life time of wire coatings and especially the corona testing of twists of enameled wires based on a frequency converter as one branch of the electrical and complex aging of insulations has a great importance – far in excess of the special field of refrigeration. The complex aging represents a combination of voltage testing technique with electrical-thermal, chemical-thermal and mechanical aging of insulating enamels. A running frequency converter yields high voltage peaks with high slew rates. Our test equipment has an intermediate circuit voltage of about 800 Vdc and a clocking frequency of 16 kHz with rectangular pulses of +/- 800 Vdc with an overshooting to max. 1,5 kVac at an edge steepness of 300 ns. The test station has a mount for 60 (!) specimen, a step less variable temperature range up to 300 °C and a fully automatically cutout of each individual wire.
The ILK offers both the manufacturing of twisted pair wires according to DIN EN 60851-5: 2009-05 and a complex aging of the specimen and also the simultaneous corona testing of 60 specimen (e. g. 6 series of 10 test samples) at a frequency converter. Based on a statistic analysis of the life time of different materials these comparative tests allow to evaluate the corona resistance of the coated insulation qualitatively and quantitatively. Complemented by microscopy investigations of the microstructure of the enamel insulation they represent an efficient test procedure for the development of materials and technologies of enameled wires.
Your Request
Further Projects
Tensile and compression testing
Determination of yield strength, tensile strength and elongation at break
Breakthrough Sensor for Adsorption Filters (BelA)
Sensor system for detecting an imminent breakthrough in gas filtration