You are here: / Home
Ice Slurry Generation
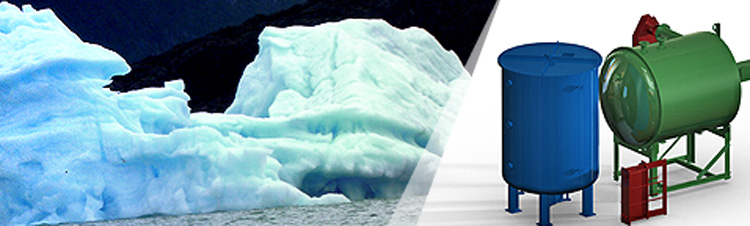
Using Direct Evaporation
... for an efficient thermal storage system, refrigeration and heat supply
Through the evaporation of single water molecules at the water surface, energy is detracted from the surrounding liquid. Because evaporation occurs in a vacuum at the triple point of about -0.5 °C, other water molecules freeze and form ice particles. The content of ice within the water-ice-mixture – the so-called ice slurry – increases with further evaporating water. This method is called vacuum ice process or also triple point process.
Based on this phenomenon, the ILK Dresden developed a process to generate an ice slurry. For this, special turbo compressors are used, developed by the ILK.
The Ice Slurry systems can have diverse applications:
- Storing cold to cover peaks in cooling demand or reduce electrical peak loads
- Implementation of cold storages extending the capacity in existing refrigeration networks and increasing the supply reliability
- Integration or rather storage of renewable energy ("Power-to-Cold")
- More flexibility of combined-heat-cold-and-power systems (Tri-Generation)
- Ice Slurry as a coolant for process cooling or air conditioning around 0 °C
- Exploration of new heat sources for heat pump applications
The technology "Flüssigeis zur Kältespeicherung" was honored by gaining 1st place at German refrigeration awards 2016.
Storing cold in ice slurry
The generation of ice slurry can be used for storing cold. In general, the use of thermal storages can lower the power peak load and the generation of refrigeration can be moved to times during which power is less expensive or “excess” renewable electric energy is available.
The ice slurry storage system has several advantages in comparison to conventional cold or ice storages:
- High energy storage density due to phase change of water resulting in compact storage modules and less dissipation
- Supreme efficiency of all processes generating ice
- No circulation of glycol required, the system can be easily integrated in (existing) cold water networks
- Consistently high capacity during the discharge process independent of the actual state of charge
- Very flexible operation: no complete discharge required before storage can be charged, quick switchover possible between charging and discharging as well as vice versa
- State of charge determinable
- ice particles are produced through the evaporation of water on the surface within the evaporator, this means compared with other ice slurry generation processes, no scraping of ice from heat exchanger surfaces – therefore less abrasion and maintenance effort
- no heat exchanger within the storage, this means capacity of storage, charging and discharging are completely independent of one another and freely selectable
- The phase change material water / ice is inexpensive, environmentally friendly and does not decompose
The ice slurry storage can be integrated in existing cold water networks or be coupled with a water chiller. While charging the storage (generation of ice slurry) the chilled water is used to dissipate the condensation heat of the process.
During high cooling demand, the cold water is chilled by melting the ice particles. This takes place within a conventional external heat exchanger. The achievable capacity of discharge can be customized to the particular application and clients’ needs by selecting an appropriate common plate heat exchanger.
Since 2014, a pilot plant has been in operation at the Westsächsische Hochschule Zwickau - University of Applied Sciences.
With a single compressor, a capacity of up to 500 kW for refrigeration or ice generation, respectively, can be achieved. The capacities of storage and discharging process can be matched to the requirements of the application.
Highly efficient ice generation
The evaporation temperature during ice generation in low vacuum is about -0.5 °C. Therefore, it is significantly higher than in conventional ice generation processes and just slightly lower than in traditional water chillers. The higher evaporation temperature results in a more efficient ice generation and the additional effort can be kept low compared to chilling water solely. The storage allows a flexible operation separated from the cooling demand. Compared to the refrigeration on demand, the efficiency can be even further increased by operating the system during nighttime at better conditions for the recooling system, see Table 2.
The use of low tariff periods, the reduction of the installed power or an increased self-consumption of less expensive and self-generated power represent further economic benefits.
Ice slurry as coolant for process cooling applications – an alternative for direct evaporating ammonium systems
The pumpable ice slurry can be used directly as coolant for process cooling. The energy storage density of ice slurry is significantly higher than those of conventional coolants. Due to the melting process, a large capacity heat sink on the cold side is provided, same as in directly evaporating systems, where, e.g., ammonium is circulated.
Ammonium (R717) is a natural, efficient and above all, in industrial refrigeration plants, a popularly used refrigerant of safety class B (toxic). However, the use of ammonium in pump-cycle systems, i.e., in refrigerated warehouses, where liquid ammonium is conveyed up to the air-cooled evaporators in cold storage, oftentimes leads to large ammonium filling quantities. Depending on the filling quantity, cost-intensive safety regulations are to be met.
Specifically regarding applications in normal coolness (positive range) the use of ice slurry is an attractive alternative compared to ammonium. Just like with the evaporation of ammonium, ice slurry guarantees a steady temperature on the cold, heat absorbing side of the air-cooled heat exchanger (air cooler). The use of ammonium as a refrigerant can be limited to the refrigeration of the engine room. The cooling distribution occurs through ice slurry.
Fields of application are:
- Industrial batch processes at 0 - 5°C
- Pharmaceutical plants
- Breweries
- Dairy plants, cheese factories
- Bakeries
- Meat and sausage processing
Heating with ice slurry
Heat pump systems are crucial components for the share increase of renewable energies and are gaining popularity. Due to low investment costs, predominately air-based heat pumps are currently used. Further disadvantages besides noise emissions are their low efficiency and operational performance during low air temperatures, meaning specifically times when heating demand is highest.
Due to the risk of frost, surface waters in our latitudes have not been used as a source of heat for heat pumps. With the ice slurry system as a first step in a cascade of heat pumps, easily accessible, natural or man-made water reservoirs exhibiting water temperatures above freezing, can be utilized as heat sources. Due to the constant and compared to air-based heat pumps, higher heat source temperature, a significant advantage in efficiency is achieved. The exploration expenditures over heat pumps, that use the ground as a source of heat, are considerably smaller.
In heat pump applications, the integration of seasonal storages might be a promising option. During the heating period, the ice content within the ice slurry storage increases continuously. In the summer, the ice slurry is used for air conditioning or process cooling, respectively.